Cross-docking in all its facets
This method of organizing logistics flows involves several perfectly controlled stages, and the various parcel routes follow a standard model in which parcels are rapidly divided thanks to a single encoding, then repackaged and redirected to the platform's exit dock for dispatch.
However, there are several possible operating modes: firstly, there is pre-distributed cross-docking, which is the classic version. Load units are managed upstream by the supplier, according to final demand. Here, it's simply a matter of receiving and dispatching orders. Then comes consolidated cross-docking, where products are managed to match end-user demands. Here, the load units received are then forwarded to a cross-docking or packaging area, where they are checked and adapted according to demand. The warehouse will need to be equipped with pallets in smaller loading units, or designed to divide goods into individual batches or merchandise kits. Finally, we have hybrid cross-docking: a more complex model that requires orders to be prepared in the packing area, taking into account products delivered by shippers and those already in the storage area. Products received can be routed to a temporary storage area, instead of going straight to cross-docking. Hybrid cross-docking is flexible and can be adapted to a multitude of situations, but it requires highly sophisticated management and organization of all logistics flows.
A number of tools are needed to manage cross-docking operations successfully: first and foremost, an information system capable of managing all functionalities and ensuring live traceability of parcels throughout the process; the production of particularly precise schedules and reception/shipment tasks; and a referencing system adapted to the simple and rapid identification of parcels. In addition, suppliers must be able to handle both preparation and packaging. Many companies have opted for cross-docking to meet the needs of an omnichannel logistics strategy.
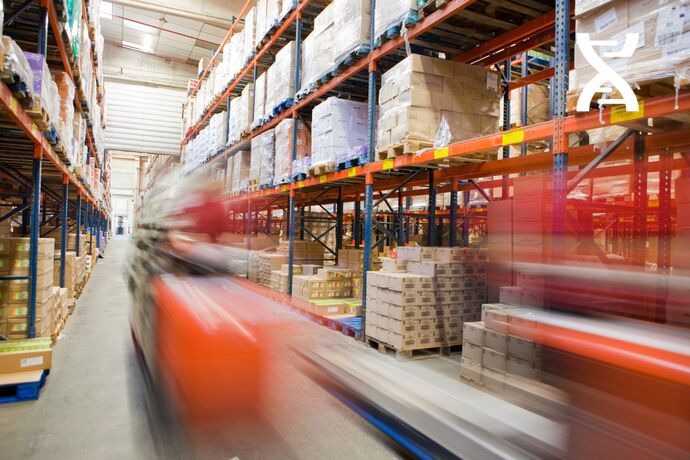