Logistics operators at the forefront of arduous working conditions
Since 2012, "pénibilité" has been defined in French labor law as "exposure to one or more occupational risk factors linked to marked physical constraints, an aggressive physical environment or certain work rhythms likely to leave lasting, identifiable and irreversible traces on health." The decree of March 30, 2011 defines 10 factors of hardship, and according to the 2002-2003 SUMER survey, 56% of employees suffer from at least one physical hardship, 4% of whom suffer from at least two. So much so, in fact, that employers are now required to open a CPP or C2P (Compte Personnel de Prévention Pénibilité) for their employees, enabling them to earn points to bring forward their retirement, reduce their working hours or retrain through professional training courses.
Unfortunately, logistics operators are no exception to this rule, as their work rhythms are physical, sustained and intense. For example, "pickers", i.e. order-pickers who have to search for goods in the warehouse according to a given list, can walk up to 15 km a day, crossing and recrossing warehouse aisles. Despite the X35-109 standard, which recommends a limit of 15 kg for objects handled by hand, operators sometimes carry up to several tonnes a day to meet ever-growing orders, with the exponential development of e-commerce, drive-throughs and click-and-collect. What's more, these repetitive tasks are particularly physically tiring for operators, who can ultimately suffer from a variety of permanent ailments, resulting in a loss of income for the company. It is acknowledged that 3/4 of all MSDs are due to 4 types of illness: elbow and shoulder tendonitis (rotator cuff injury, well known among cashiers), carpal tunnel syndrome (common among people who handle the computer mouse on a daily basis), and back problems universally found in all physically demanding professions. At the end of the working day, these order-pickers end up bent over, exhausted and complaining of various aches and pains, resulting in an absenteeism rate that is detrimental to business activity, not to mention the poor image conveyed regarding human resources management.
However, solutions do exist to greatly reduce these painful factors in warehouse management. As technologies are deployed, working conditions are improving to facilitate operators' tasks, as detailed below.
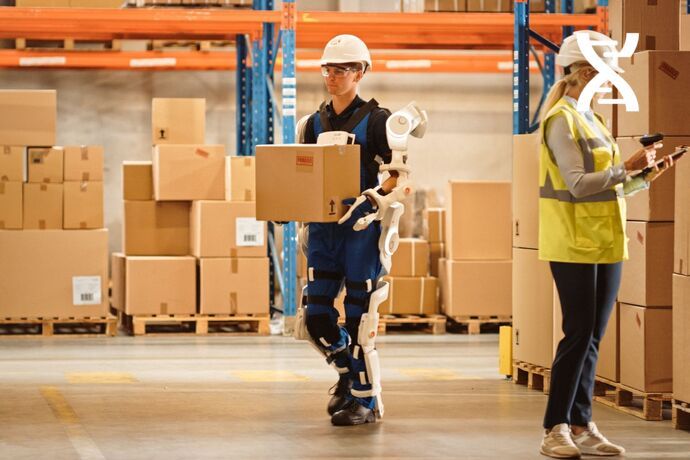