Supply chain management
Definition
Procurement as a business term means buying goods, whether for sale, for use in the manufacture of products, or for storage. A company's profitability largely depends on its supply management. On average, supplies account for half the cost of the merchandise offered for sale.
Different methods: empirical, just-in-time, kanban?
there are, of course, a number of different procurement methods, based on different management approaches. The empirical procurement method is based on historical sales data, analyzing sales to better understand purchasing behavior. The "just-in-time" or kanban (Japanese for "label") method, in which downstream suppliers order upstream suppliers, means that we only produce on demand. This means just-in-time production, which limits the volume of inventory, but also demands a high level of responsiveness. The aim is to size inventories as precisely as possible (no longer relying on safety stocks) so as to reduce costs. In fact, Kanban is better suited to the manufacture of mass-produced items, as opposed to the MRP (Material Requirement Planning) method of push-flow systems (the flow is pushed towards the customer), where production is based on anticipated demand, whereas the Just-in-Time method is based on a firm order, drawn up by the customer.
Supply chain points: factory, plant, warehouse
Next comes the management of supply chain "points": between factories and points of sale, there are a multitude of intermediate points such as central warehouses, overflow warehouses, regional depots, hubs, platforms, etc., of varying sizes depending on their function and location in the chain, and which need to be optimally managed to avoid generating extra costs.
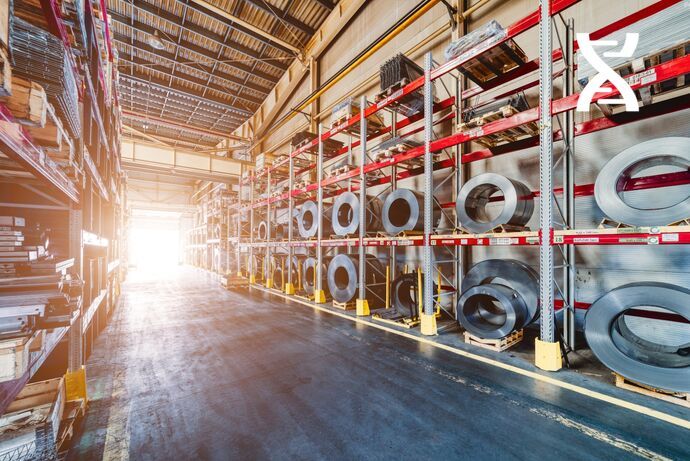