Reverse logistics, between legal obligation and customer satisfaction
After developing delivery solutions designed to optimize the customer experience, e-commerce players are now focusing their efforts on reverse logistics. But beyond customer satisfaction, the challenge for online retailers is also to meet their legal obligations.
Above all, a legal obligation
Under article 221-18 of the French Consumer Code, "consumers have a period of fourteen days to exercise their right of withdrawal from a contract concluded at a distance".
An argument for customer satisfaction
This legal obligation is undoubtedly in the interests of customer satisfaction. Knowing that they have this freedom will encourage consumers to order more easily.
Costs not to be underestimated
Shipping costs for the first shipment, transport costs for the returned parcel, processing of the returned parcel, reshipment of a new product - these are just some of the costs involved in returning a product Managing returns is therefore a highly strategic issue for e-tailers, as it represents a significant cost. To limit these costs, e-tailers need to simplify their returns policy as much as possible, and limit the number of interactions between the consumer and customer service.
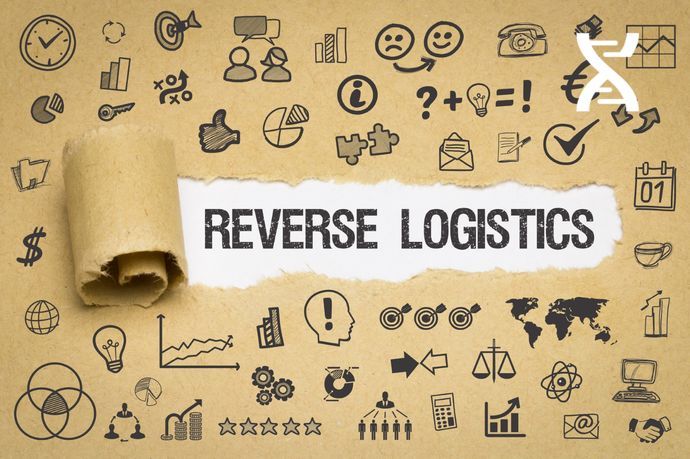